Laser marking of a data matrix on cardboard/shipping box
- PT Asia
- Apr 16, 2020
- 2 min read

Laser marking of a data matrix on cardboard/shipping box | CO2 Laser by Macsa ID | for logistics traceability.
Macsa id success story in the logistics sector
Client: TVH
Country: Belgium
Industry: Automation Logistics
Application: Datamatrix
Substrate: Cardboard
Laser solution: SPA C10 with beam expander – 17 lasers installed
Company intro and history
TVH is a global supplier of parts and accessories for material handling, industrial and agricultural equipment with customers in more than 170 countries, and has been split up into two business units: TVH Parts and TVH Equipment. As a company, they continually invest in their automation and optimisation of their logistics processes to improve their service.
With their headquarters based in Waregem, Belgium, they got in contact with Codipack, exclusive distributors for Macsa ID in this country.
Challenge
Due to open a new logistics centre, the client was looking for an up-to-date coding solution. In their old logistics centre they use a print and apply machine for this application. The client’s idea was to install two print and apply machines to apply a two-dimensional, unique code on two sides of each box. Each code contains ten numeric numbers, and roughly sized at 12mm x 12mm. The purpose of the code is to identify each carton throughout the logistic process, all the way until it is shipped.
For example, once a box is identi ed by a reader/scanner, it continues to the picking division. There, the same, unique code is scanned again and lled with the assigned products. In the next step, once the code is scanned the shipping list is added. After that, the scanned code identi es which cover needs to be added. In the nal step, the unchanged code indicates which shipping label needs to be applied to the box.
Given its importance at every stage of the process, the quality and readability of the marking was vital.
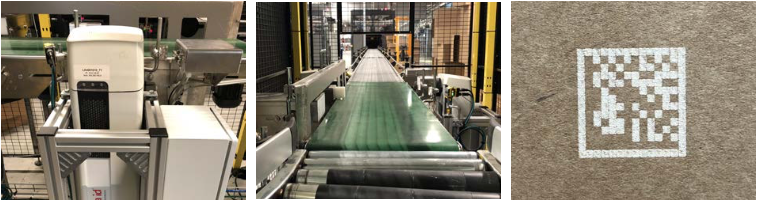
Macsa id solution
After having been presented with both laser and inkjet printing options, both machines were installed on a test line over a three-month period. Once the testing period was complete, the laser solution was more reliable and had a better total cost of ownership.
The laser solution was successful in the end thanks to:
No consumables being required with laser, representing a potential saving of 140,000,000 labels per year for the client
No stoppages on the production line due to label roll replacements
No more unplanned productions stoppages or losses
A total of sixteen lasers were installed across eight production lines, with two being on each one. A spare laser was included as part of the solution in case of any emergencies.The installation runs 24/7and produces on average:
192,000 cartons per day
1,344,000 cartons per week
70 million cartons per year
Macsa ID won this project ahead of its competitor in this case thanks to its state-of-the-art design, the technical service available, and the modular design which allows for the laser tube or head to be changed with minimal fuss.
Comentários