Laser coding on cardboard boxes by 30W CO2 lasers
- PT Asia
- Jan 19, 2021
- 2 min read

Laser coding on cardboard boxes
KH Lloreda started its activity in 1949 far from the world of detergent manufacturing. It manufactured all kinds of metal coatings and had such an effective product to clean the parts to be delivered to its customers that it led its founder to formulate his own cleaning products, including its star product, KH-7.
As the formulas developed later proved to be highly effective, they were marketed in the industrial sector and in the mass market, which changed the history and direction of the company.
THE CHALLENGE
The challenge proposed by KH7 Lloreda, the current leader in the Spanish market for kitchen cleaners and stain removers, was to install a box printing system to carry out the marking of its secondary packaging. This should be integrated into the same production line, allowing it to be customized and perform an automatic format changeover, without having to make adjustments when changing the product.
MACSA ID SOLUTION
For the lateral and frontal marking of the boxes containing the detergent bottles, Macsa id integrated two 30W CO2 lasers (Macsa id SPA CB 30) in its own production line. For this reason, a laser marking station was installed in order to be able to mark the two adjacent sides of the crate. Finally, in order to obtain a high quality of printing, the customer was recommended to carry out the printing in static, for which three stops were placed synchronized with the laser equipment that regulate the passage of the boxes.
Laser marking on cardboard is one of the most common materials used in the coding market. In this case, with the equipment installed and a reserve of laser additive on the cardboard, the appropriate contrast for the codes to be read correctly was achieved, thus regulating the power and speed of the scanners to achieve a clear legible black marking on the white cardboard, including all the elements that comprise the coding.
The solution also includes both the Marca software by Macsa id to design the messages marked on the boxes, and the Integra Optima software. The latter, which is integrated into the customer's ERP, centralizes the entire coding and marking process in a single point, drastically reducing the number of interventions, and as a result, the possibilities of error from human intervention.
Thanks to the solution provided by Macsa id, the customer has obtained a high-performance marking system that does not cause production stoppages, as it does not use continuous replacement consumables.
Have you thought that by centralizing the coding and marking process in a single point you optimize resources, speed up processes and control the coding and verification systems?
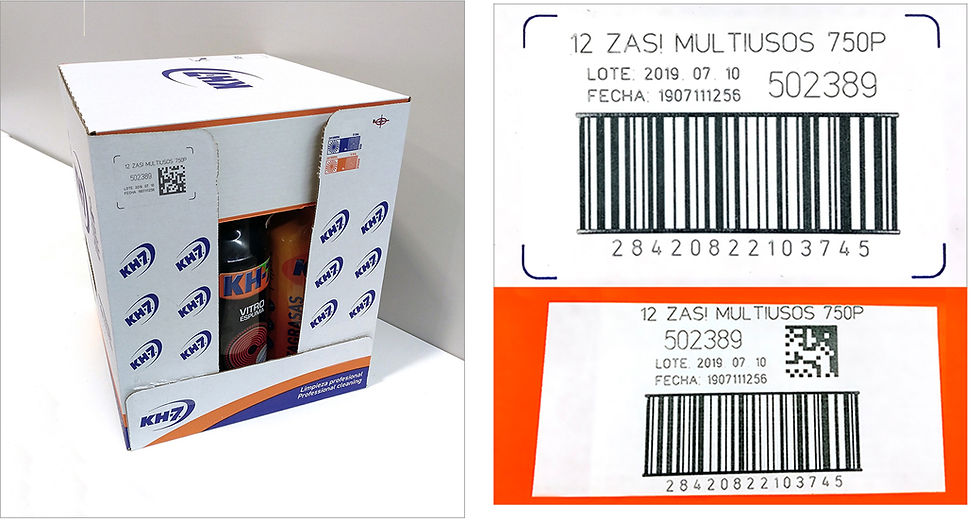
Comentarios